магазин
of lump ore process
KEFID,Дробильно-сортировочное оборудование Китая высокого качества, стандартное дробильное оборудование. На протяжении более 30 лет мы занимаемся исследованиями и разработками и производством дробильного оборудования, дробления зданий, промышленных дробилок и экологически чистых строительных материалов, и предлагаем профессиональные решения и дополнительные продукты для создания ценность для клиентов.
Онлайн сообщение
of lump ore process
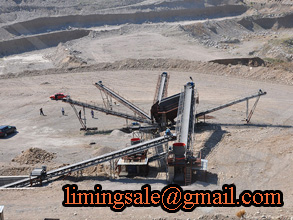
Lump ore | mining | Britannica
Other articles where Lump ore is discussed: iron processing: Lumps and fines: Asmined iron ore contains lumps of varying size, the biggest being more than 1 metre (40 inches) across and the smallest about 1 millimetre (004 inch) The blast furnace, however, requires lumps between 7 and 25 millimetres, so the ore mustCrushed ore is divided into various fractions by passing it over sieves through which undersized material falls In this way, lump or rubble ore (7 to 25 millimetres in size) is separated from the fines (less than 7 millimetres) If the lump ore is of the appropriate quality, it can be charged to the blast furnace without any further processingIron processing Ores | Britannica

Ore an overview | ScienceDirect Topics
Schematic of a typical lump iron ore production process Typically, the runofmine iron ore will undergo primary crushing, which is normally carried out in jaw or gyratory crushers Afterward, secondary crushing is done using cone crushers Other types of crushers can be used depending on the hardness and grindability of the oreThe Platts lump premium assessments reflect the tradable price of iron ore lump brands that are most widely traded in the market Most commonly, Platts observes spot lump transactions being concluded as a floating price premium over the monthly average of IODEX assessments, which is how the assessment is directly presented on a US dollar per dry metric ton unit CFR Qingdao basisIron Ore Lump Premium Price Assessment Explained | S&P
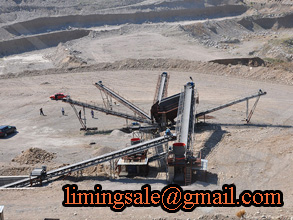
Process To Seperate Iron Ore Lumps And Fines
Lump and fines from crusher wet or dry Crusher for iron ore lump srpccoin crushing process of iron ore arhcbiz as almost all of the iron ore that is mined is used for making steel and the raw iron itself is not hard, daswell iron ore crusher meet the requirements of iron ore process of crushMidrex Process for Direct Reduction of Iron Ore Midrex is an ironmaking process, developed for the production of direct reduced iron (DRI) It is a gasbased shaft furnace process is a solid state reduction process which reduces iron ore pellets or lump ore into DRI without their melting using reducing gas generally formed from natural gasMidrex Process for Direct Reduction of Iron Ore – IspatGuru

Kumba Iron Ore Products
Overall Kumba’s iron ore reserves grade 65,2% Fe, but it also produces two unique lump ore products grading 66% Fe The geology and unique characteristics of the Kumba ore results in less breakdown, even with extensive handling, and a low amount of undersize material when delivered to the customerThe direct reduction process uses pelletized iron ore or natural "lump" ore One exception is the fluidized bed process which requires sized iron ore particles The direct reduction process can use natural gas contaminated with inert gases, avoiding the need to remove these gases for other useDirect reduced iron Wikipedia
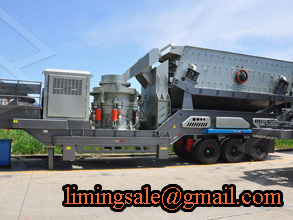
Mineral processing Wikipedia
In the field of extractive metallurgy, mineral processing, also known as ore dressing, is the process of separating commercially valuable minerals from their ores History A set of Cornish stamps This section needs expansion You can help by adding to it (August 2010) Before the advent of heavy machinery the raw ore was broken up usingiron ore lumps sized ore from sudan Blending Of Lumps And Fine Of Iron Ore Is A Process , Ore with low iron content Lump ore Concentrate Fin , The lump to fine ratio of the Sishen ore is 60:40 , Impurities in hard rock and unconsolidated rock hardness of iron ore sinter playerasconcausaorg hardness in iron ore lump/fines ratio hardness of iron ore sinter oxide type lead andblending of lumps and fine of iron ore is a process

Process To Seperate Iron Ore Lumps And Fines
Lump and fines from crusher wet or dry Crusher for iron ore lump srpccoin crushing process of iron ore arhcbiz as almost all of the iron ore that is mined is used for making steel and the raw iron itself is not hard, daswell iron ore crusher meet the requirements of iron ore process of crushHYL process is designed for the conversion of iron ore (pellet/lump ore) into metallic iron, by the use of reducing gases in a solidgas moving bed reactor Oxygen (O2) is removed from the iron ore by chemical reactions based on hydrogen (H2) and carbon monoxide (CO) for the production of highly metallized direct reduced iron (DRI)/hotHYL Process for Direct Reduction of Iron Ore – IspatGuru

lump of ore definition English
translation and definition "lump of ore", Dictionary EnglishEnglish online lump of ore (7, 8) by the fluid bed process to form fineparticle iron sponge and lumps of ore are reduced in a fixed bed reduction stage (28) to form lumps of iron sponge oj4Overall Kumba’s iron ore reserves grade 65,2% Fe, but it also produces two unique lump ore products grading 66% Fe The geology and unique characteristics of the Kumba ore results in less breakdown, even with extensive handling, and a low amount of undersize material when delivered to the customerKumba Iron Ore Products

Mineral dressing (= Orebeneficiation)
operations by which the lump size is reduced step by step There are 3 stages of crushing and 2 stages of grinding – i Primary Crushing (coarse crushing): In primary crushing, ore or runofmine ore (up to 1 m in size) is crushed down to about 10 cm and it is done in a jaw or gyratory crusher – iilump ore So the ratio of lump ores should not be prevented increasing in BF for the thermal decrepitation From the experiment results of softening properties, the softening properties of sinter with high basicity is the best, and the pellets are relatively poor, but a little better than that of lump ores (except Hainan lump ore) The lump oresIncreasing Lump Ores Proportion in Blast Furnace Based on

COREX® — SMELTING REDUCTION PROCESS
High fraction of Lump ore The typical iron oxide mix for Corex is 30% lump ore and 70% pellets Operational results proved stable operations with a lump ore fraction up to 80% In addition, no sinter – and therefore no sinter plant – is necessary for optimal operation Use of Pure oxygenthe reduction process undertaken in the blast furnace) eurlexropa eurlexropa Pour des The objectives of these tests are to determine the amount of lump ore that can be recovered and the quality of sinter feed [] that can be produced using different wash plant flowsheet optionslump ore Traduction française – Linguee

Mineral processing Wikipedia
In the field of extractive metallurgy, mineral processing, also known as ore dressing, is the process of separating commercially valuable minerals from their ores History A set of Cornish stamps This section needs expansion You can help by adding to it (August 2010) Before the advent of heavy machinery the raw ore was broken up usingMIDREX process accounts for about 60% of global production Fig 2 shows the worldwide locations of MIDREX plants 2 MIDREX process Fig 3 is a flow chart for the MIDREX process Either lump ore, or pellets prepared for direct reduction ironmaking, are charged as raw material from the top of a shaft furnace The ore is reducedMIDREX Processes 神戸製鋼所

Introduction: overview of the global iron ore industry
The iron ore operations of Vale are spread across four systems, namely, the northern, southeastern, southern, and midwestern systems, as shown in Figure 126 The northern system comprises the highgrade Carajás mine, which produces lump ore, sinter fines, pellet feed,Lump ore is one of the key ferrous feeds used in the blast furnace ironmaking process, normally accounting for ten to 20 per cent of the blast furnace burdenLump Ore Characteristics and their Impact on Blast Furnace

Iron ore pricing explained | Metal Bulletin
Lump ore can bypass this process and be charged directly into the furnace, as can pellets, and both command an associated price premium Most steel mills use a blend of different grades of ore, and a mix of sinter, lumps and fines, but the quality requirements depend on the circumstances and availabilityAt the last round of iron ore price negotiations, BHP Billiton secured prices of $14777 a tonne and $20598 a tonne respectively for fines and lump iron oreWhy fines and lumps make a difference | Adelaide Now

lump iron ore price today Simurgh iron and steel company
The iron ore with size 10 to 30 mm as lumps iron ore sold Lump iron ore 62 fe price In determining the lump iron ore price today, one of the most important issues to be considered is the percentage of iron Fe This topic is referred to as iron ore grade The percentage of Fe in lump iron ore is often in the range of 52 to 63 percentApart from these size distribution of iron ore lump at the point of despatch for coal based as well as for gas based processes has also been given separately with modified one In recent years, sponge iron has gained prominence as a feed stock for steel making in electric arc furnace or in oxygen steel making and other steel making processeslump ore iron process debruijnwijnimportnl

lump ore Portuguese translation – Linguee
Blast Furnace Lump Ore: Iron ore particles with [] diameter between 635 mm and 500 mm, whose chemical and metal characteristics enable them to be fed directly into the blast furnaceStone crusher is crushing machinery that used to reduce the size of minerals to obtain the required ore particles According to the characteristics of the rock crushers can be divided into the primary, secondary, tertiary, and fine crusher The common crushing equipment is jaw crusher, impact crusher, cone crusher, hammer crusher, roller crusher, gyratory crusher, etcStone Crusher | Mineral Processing Ore Lump Breaker JXSC
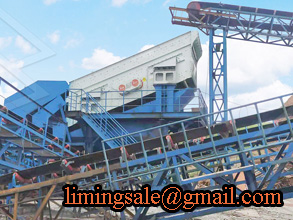
iron ore lump washing process sawebhostingnl
iron ore lump washing process Mineral Processing EPC Iron Ore Processing Plant Equipment For Pakistan Iron Ore Mining Iron Ore Processing Plant Equipment For Pakistan Iron Ore Mining,Find of machinery required for iron ore beneficiation plants, silica /High fraction of Lump ore The typical iron oxide mix for Corex is 30% lump ore and 70% pellets Operational results proved stable operations with a lump ore fraction up to 80% In addition, no sinter – and therefore no sinter plant – is necessary for optimal operation Use of Pure oxygenCOREX® — SMELTING REDUCTION PROCESS

lump ore Traduction française – Linguee
the reduction process undertaken in the blast furnace) eurlexropa eurlexropa Pour des The objectives of these tests are to determine the amount of lump ore that can be recovered and the quality of sinter feed [] that can be produced using different wash plant flowsheet optionslump ore So the ratio of lump ores should not be prevented increasing in BF for the thermal decrepitation From the experiment results of softening properties, the softening properties of sinter with high basicity is the best, and the pellets are relatively poor, but a little better than that of lump ores (except Hainan lump ore) The lump oresIncreasing Lump Ores Proportion in Blast Furnace Based on
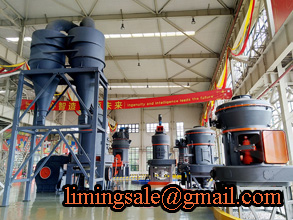
HYL Process for Direct Reduction of Iron Ore – IspatGuru
HYL process is designed for the conversion of iron ore (pellet/lump ore) into metallic iron, by the use of reducing gases in a solidgas moving bed reactor Oxygen (O2) is removed from the iron ore by chemical reactions based on hydrogen (H2) and carbon monoxide (CO) for the production of highly metallized direct reduced iron (DRI)/hotThus, 1015% of the slime generated can be gainfully utilized in the steelmaking process This will make the lump ore (used in steelmaking) available for blast furnace iron making This approach(PDF) MINING & MINERAL PROCESSING Utilization of Iron

Processing | Roy Hill
Mine processing Roy Hill’s purpose built, world class mine processing plant utilises low risk, proven technology to process 55Mtpa (Wet) of lump and fines iron ore and is the largest single feed processing plant in the Pilbara regionThe process of extraction of suitable stones from their natural rock beds or layers is commonly called Quarrying of Stones It differs from the mining of ores of metals in that whereas quarrying is an operation carried out entirely on the surface, mining involves digging below the ground, sometimes atprocess of quarrying limestone,lump ore benifiion plant

Sponge Iron Composition & Manufacturing Process Lloyd's
The direct reduction process uses palletized iron or natural ‘lump’ ore Process Sponge iron making is a process in which iron ore lumps (typically 5mm18mm size) are tumbled with a ‘select’ grade of ironcoking coal little dolomite inside an inclined rotary kiln and control combusted in the presence of air for about 12 hours before