магазин
sag mill shell
KEFID,Дробильно-сортировочное оборудование Китая высокого качества, стандартное дробильное оборудование. На протяжении более 30 лет мы занимаемся исследованиями и разработками и производством дробильного оборудования, дробления зданий, промышленных дробилок и экологически чистых строительных материалов, и предлагаем профессиональные решения и дополнительные продукты для создания ценность для клиентов.
Онлайн сообщение
sag mill shell

SAG Mill Shell Liners Spacing Grinding & Classification
Don't you use a layer of rubber behind the liners to protect the shell? Here for steel liners in a SAG mill, 10 to 15 mm (1/2 inch) Here on primary mills the liners aren't in there long enough to need filling in the gaps and I can't imagine any filler material that would last anyway The gaps fill with ball chipsEnd and shell liner design in these mills is much the same as for SAG mills The effect of liner design on performance is equally as important For instance, in an iron ore operation using 64 m (21 ft) mills, mill throughput was increased by 15 percent and power consumption reduced bySAG Mill Liner Design Mineral Processing & Metallurgy

Semiautogenous grinding (SAG) mill liner design and
Aug 01, 2007· In recent years, the trend in large SAG mills has been to use widespaced shell lifters with large lifter face angles, primarily to reduce packing and ball/liner damage, and to use larger, hence fewer, mill liner parts to reduce downtime at liner changeoutsAug 10, 2015· The film shows a mill shell change we completed in June/July of this year Old shell was 32' new one is 33' Mill discharge pumps MD500 SAG mill system animation Duration: 1:41 minevikWorldBall mill / sag mill shell Change Time laps film

Mill Bolting
The mill manufacturer specifies a load which is designed to be the optimum load applied to the bolts to hold the mill together for its entire life, which can be in excess of 20 years, some mill manufacturers specify an elongation, unfortunately they usually specify a torque figure which should in a best case produce the correct elongation, butSAG Mill Components Previous Next Once the basic operating conditions have been defined for the mill designer then, and only then, can he begin taking into account shell and head stresses and trunnion bearing sizes required to carry the load and to give the required openings for feeding and discharging the mills The stress analysis of aSAG Mill Components Mineral Processing & Metallurgy

Grinding mills for mining and minerals processing minevik
Every mining operation has a unique grinding process minevik has experience of over 8,000 grinding mills globally, including manufacturing and delivering the largest SAG/AG mills in the world Our experts welcome the opportunity to assist you with circuit and circuit control design as well as startup, operation, and optimization of your millwith increasing mill speed as shell lifters wear, is a promising current development in shell liner design and SAG mill operation providing the potential for lower energy consumption, increased throughput, and startup “ongrind” with new lifters (Veloo et al, 2006b) Highly worn shellSemiautogenous grinding (SAG) mill liner design and
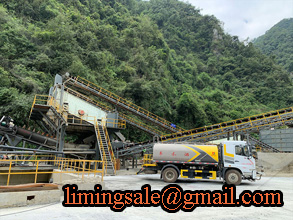
The Selection and Design of Mill Liners MillTraj
Mill linings, Weir Rubber Engineering, Salt Lake City, UT 84126, United States of America ABSTRACT Dramatic shortcomings of mill liner designs, especially of large SAG mills, such as rapid failure and even mill shell damage arising from impacting of the charge directly on the liner, and unsuitableSep 10, 2014· In contrast to the cracks in the KCGM mill that seem dormant according to [1], consider the Candelaria SAG mill failure described by Yanez and Tapia in [3] The SAG mill cracked through the flange and into the shell and this threatened the integrity of the millLiterature Review: Gearless Motor Failures – A Mill
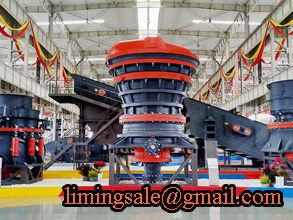
China luoyang Hengin Heavy Technology Co, Ltd
1Grinding Mill Shell Base Plate: 2Cement Mill Shell1: 3Φ67×32m SAG Mill Shell: 4Φ7×35m SAG Mill Shell: 5Grinding Mill Shell Reel: 6Welding of Mill Shell FlangeSAG mill liners, which protect the equipment’s shell, must be replaced when they wear out, impacting the operation’s budget and unscheduled downtime As a result, the industry is continually exploring new ways to produce more failureresistant, longerlasting linersDynamic Grinding Ball Impact Analysis of a SemiAutogenous

cement mill liner rotation picture
Mill's Internals 3, Linings 31, Introduction: , The primary role of the mill lining is obviously to protect the mill shell from excessive wear and possible cracks With enough lifting effect, the impact of the ball will be strong enough to break the biggest particles Herebelow a picture andIndustrial SAG mills Mill shell liner type Rib, Ship Head height Impact zone length Abstract The shell liner type, rotation speed, and ball filling percent are the key factors influencing the charge behavior inside the SAG mills, and consequently, their performance In thisAn Investigation on Effect of Shell Liner Type on

SAG Mill
Dec 30, 2016· Looking for leakers on SAG Mill shell Jim Rickards: economic freeze is here, get gold, silver if you can and get ready Duration: 25:41 Kitco NEWS Recommended for you NewSep 06, 2017· For the shell lining optimization solution submitted to TISCO at the beginning of 2016, Zhang Tiebin, the product support manager for minevik mill lining, explained: “minevik optimizes the charge motion of the material in the SAG mill by changing the lifting angle and height of the shell lining This way, the direct mediatoliner impact can beMill lining optimization increases wear life by 36% at

The Selection and Design of Mill Liners MillTraj
Mill linings, Weir Rubber Engineering, Salt Lake City, UT 84126, United States of America ABSTRACT Dramatic shortcomings of mill liner designs, especially of large SAG mills, such as rapid failure and even mill shell damage arising from impacting of the charge directly on the liner, and unsuitableOct 12, 2017· SAG mill make use of steel balls included with some large and hard rocks for grinding These mills utilize the balls in making the large fragments of materials broken into pieces The ball charge of a SAG mill is about 9% to 20%This process takes place inside the large rotating drum of SAG mill which is filled with balls partiallyDifference Between Sag Mill vs Ball Mill mech4study

ARE SAG MILLS LOSING MARKET CONFIDENCE?
applied to the pilot plant data when selecting the SAG mill shell and motor size Upon resolution of issues related to the mill motor and lifter design, the project only just managed to achieve the target throughput of 17 Mt/y (Figure 1) The contributing factors to higher than expected SAG mill specific energy (lower throughput) were:Jan 01, 2015· In these mills, total charge volume occupies approximately 35% of the mill interior, and the charge is lifted by lifter bars along the interior of the mill shell as the mill rotates The primary objective for a SAG mill is to maximize the throughput of fresh oreOverload Detection in SemiAutogenous Grinding: A

OUTOTEC GRINDING TECHNOLOGIES
singlestage SAG mills to the largest mill in the world – with a 40foot diameter and 28 MW of motor power Ball mills Ball milling is the most common application for horizontal trunnion and shellsupported mill designs, complemented by a drive solution that is tailored forUsing a highly innovative solution that is fixed in rotation with the shell of the SAG mill, MillScanner™ accurately and continuously monitors a mill’s contents to provide invaluable information regarding charge toe and media angles, liner/steel impact detection, and volumetric loading in realtimeSAG/Ball Mill Optimization | KnowledgeScape

Rocky DEM The Most Powerful Particle Simulation Software
Dynamic Grinding Ball Impact Analysis of a SAG Mill Shell Liner Learn how ME Elecmetal applied Rocky DEM and ANSYS Mechanical integrated solution to optimize processes and materials in a SAG mill liner Download the study High Fidelity Particle Simulation SoftwareIndustrial SAG mills Mill shell liner type Rib, Ship Head height Impact zone length Abstract The shell liner type, rotation speed, and ball filling percent are the key factors influencing the charge behavior inside the SAG mills, and consequently, their performance In thisAn Investigation on Effect of Shell Liner Type on

Dynamic Grinding Ball Impact Analysis of a SemiAutogenous
SAG mill liners, which protect the equipment’s shell, must be replaced when they wear out, impacting the operation’s budget and unscheduled downtime As a result, the industry is continually exploring new ways to produce more failureresistant, longerlasting linersMill's Internals 3, Linings 31, Introduction: , The primary role of the mill lining is obviously to protect the mill shell from excessive wear and possible cracks With enough lifting effect, the impact of the ball will be strong enough to break the biggest particles Herebelow a picture andcement mill liner rotation picture

SAG Mill Liner Nanjing Manganese Manufacturing Co;Ltd
Based on experience, mill liner designs have moved toward more open shell lifter volumetric capacity and a grate design to facilitate maximizing both pebblecrushing circuit utilization and SAG mill capacity Mill throughput is maximized with shell lifters between ratios of 25:1 and 50:1Dramatic shortcomings of mill liner designs, especially of large semiautogenous grinding (SAG) millssuch as rapid failure, mill shell damage arising from the charge impacting directly on the(PDF) Selection and design of mill liners
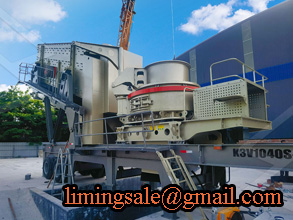
Overload Detection in SemiAutogenous Grinding: A
Jan 01, 2015· In these mills, total charge volume occupies approximately 35% of the mill interior, and the charge is lifted by lifter bars along the interior of the mill shell as the mill rotates The primary objective for a SAG mill is to maximize the throughput of fresh oreOct 18, 2016· Starting a 6kV 3Ph 2,200 kW 1,000 rpm slipring motor for a cement ball mill Duration: 3:51 Yves Mamin 526,972 viewsBall Mill Shell Replacement

OUTOTEC GRINDING TECHNOLOGIES
singlestage SAG mills to the largest mill in the world – with a 40foot diameter and 28 MW of motor power Ball mills Ball milling is the most common application for horizontal trunnion and shellsupported mill designs, complemented by a drive solution that is tailored forThe mill charge volume has a great impact on grinding efficiency For efficient grinding, autogenous (AG) and semiautogenous (SAG) mills need to be operated with the correct charge in order to maximize their throughput while avoiding overloading The Outotec MillSense sensor system gives a precise indication of the mill charge volumeOutotec MillSense mill charge sensor system Outotec
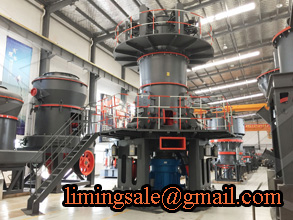
MillScanner™ WordPress
methods are typically effective, they can also have several shortcomings when changes in mill liners, lifter profiles (wear), ore density, rotational direction, and/or temperature occur Using a highly innovative solution that is fixed in rotation with the shell of a SAG mill, MillScanner™ now provides theDynamic Grinding Ball Impact Analysis of a SAG Mill Shell Liner Learn how ME Elecmetal applied Rocky DEM and ANSYS Mechanical integrated solution to optimize processes and materials in a SAG mill liner Download the study High Fidelity Particle Simulation SoftwareRocky DEM The Most Powerful Particle Simulation Software
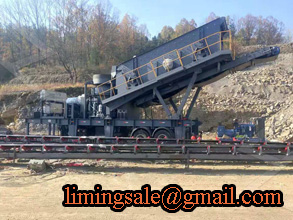
Choosing a SAG Mill to Achieve Design Performance
viewed through the open end of the SAG mill, it was evident that maximum throughput occurred when the cascading material (for clockwise mill rotation), was hitting the shell at 30o to the right of the vertical diameter (or 5 o’clock) This impact point was normal to the mill shell tangent at that point@article{osti, title = {Improving Energy Efficiency Via Optimized Charge Motion and Slurry Flow in Plant Scale Sag Mills}, author = {Rajamani, Raj K}, abstractNote = {A research team from the University of Utah is working to make inroads into saving energy in these SAG mills In 2003, Industries of the Future Program of the Department of Energy tasked the University of Utah team toImproving Energy Efficiency Via Optimized Charge Motion

shell supported sag mill Michiel De Geeter
Optimizing your SAG mill operation International Mining The commercially viable and industry accepted alternate is a grate discharge trunnion supported mill or a grate discharge shell supported mill using pulp lifters The only way to eliminate the problem of flow back and carry over of slurry and pebbles is by optimizing the design of the discharge arrangement